4 min read
Assembling Your Thermoformed Product: Sourcing the Best Materials & Accessing the Right Suppliers
By: David O'leary on May 10, 2023 9:00:00 AM
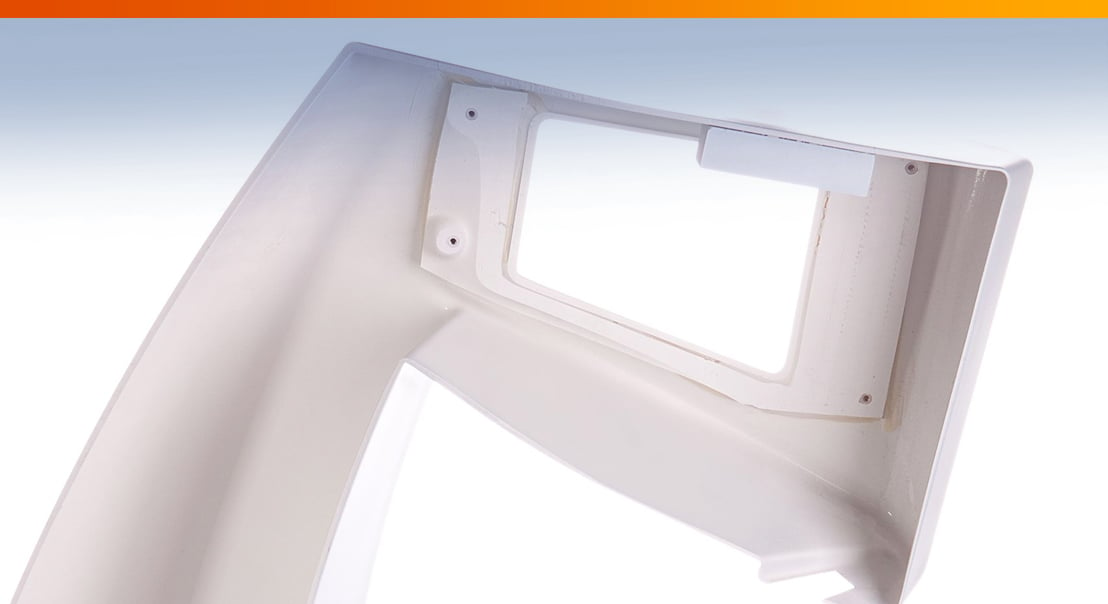
In this bullish economy, designers face more than just the usual challenges when developing a product. The manufacturing sector is rebounding, but there are residual effects left over from the economic disruptions of the last few years. Deloitte notes that manufacturing resilience gained momentum since 2021, but near-term indications aren’t entirely positive.
Supply chain disruptions still linger with rising inflation and labor shortages putting additional strain on product lead times. Finding the right strategy when bringing a product to market (or optimizing an existing range to maintain profitability), starts with sourcing the best materials and accessing the right suppliers. Concepts like “Design-to-Cost” and “Design-for-Manufacturing-and-Assembly” regularly feature in today’s product design briefs, putting the onus on developers to investigate every facet of the product’s viability across its lifecycle before considering a launch.
When conventional manufacturing techniques cannot solve your current production challenges, a thermoformed product may just be the solution you’ve been looking for. Let’s look at why this manufacturing and assembly approach may be right for you.
Overcoming Material Sourcing and Supply Chain Challenges with a Thermoformed Product
Cost pressures are just one of many reasons why a product fails in the market. Given the current struggles with sourcing materials, finding the right “bed-fellows”, and optimizing the design for cost, developers have to clear a series of hurdles to prove a product’s viability.
Collaborating with a manufacturing team earlier in the process will help circumnavigate the existential issues that may put a project in jeopardy. In the same report from Deloitte (that we linked above), they identify five key trends that will shape product manufacturing in the coming years. The three trends that stand out are:
- Technology – Increased investment in tech creates an environment that remains agile and can deal with a shifting economic climate
- Talent – Where technology cannot solve an issue, accessing talent becomes a priority that only expert suppliers may be able to overcome
- Supply chain – Effective management of materials, minimizing production cycle times, and ensuring part-to-part repeatability is vital to establishing a viable product range
Along with these three trends, smarter factories and sustainable (or ESG-compliant) product lines are key operational drivers for future success, according to Deloitte. When it comes to shortening the project runway (or limiting costs), ensuring quality (maintaining compliance), and delivering on time (meeting demand), here are three ways you can set your project up for success.
Material Sourcing and Management
Prices for PE (polyethylene) and PP (polypropylene) will remain under pressure in the U.S. during 2023, but you should also consider the lead time required for sourcing materials. Lower volume product runs are susceptible to price fluctuations that could increase the cost per unit, while suppliers may also insist on a minimum buy just to consider your order.
Working with Kenson Plastics gives you access to our supplier network, and the ability to leverage our buying power for improved pricing. We buy in bulk, ensuring that we have the material available when you need it. Kenson Plastics can also recommend different materials you can use if we understand the application of the product and the environmental variables inherent in your design.
Reducing Waste and Improving Cycle Time
When reviewing the design, you need to look for opportunities to improve the manufacturability of the parts while limiting material waste. With a bit of design ingenuity, you can find a manufacturing and assembly process that conforms to your specifications but also improves the cycle time and maintains the quality of the part.
Kenson Plastics leverages our decades of experience and the lessons learned from complex manufacturing projects to support you every step of the way. We have a dedicated tech center that ensures we maintain the tight tolerance stack you require, and validates each part to verify it complies with your specifications.
Custom Thermoforming Turnkey Manufacturing and Assembly
A growing trend among product designers is to outsource the manufacturing and assembly process to a single partner. The benefits of moving to a turnkey manufacturing model include reduced labor costs, access to specialized skills, and increased productivity. This manufacturing approach also insulates you from market fluctuations, maintaining your competitiveness even when there are changes in demand.
At Kenson Plastics, we strive to develop a beneficial relationship with our customers. The earlier we become part of the project, the more value we can add. By partnering with us, you can mitigate the current risks in the market and develop a viable manufacturing process for low-volume, high-quality plastic products.
Ensuring Prosperity with Manufacturing Solutions from Kenson Plastics
Kenson Plastics is a one-stop manufacturing partner. We can provide end-to-end support including design review and material selection, manufacturing process optimization, and quality validation that ensures part-to-part repeatability. We’re a family-owned business that likes to take on projects other manufacturers would prefer to avoid. Because of our size, we can insulate you from today’s fluctuating market conditions and reduce your lead times.
To source the best materials and access the right suppliers for your thermoformed products, send us a message to start the conversation.
Related Posts
Outsource Thermoformed Product Assembly to Reduce Labor-Intensive Operations
A professor at MIT, Jonathan Byrnes, is famous for saying that most supply chains are great at...
Hard Tooling vs Soft Tooling for Manufacturing Durable High-Precision Parts
Design teams face many challenges when bringing a new product to market. While product features,...
How to Improve Lead Times for Thermoformed Parts
Improving lead times is how manufacturers maintain a competitive edge in today’s economic...