A professor at MIT, Jonathan Byrnes, is famous for saying that most supply chains are great at catering to the needs of the business 20 years ago.
Over the last few years, many companies had to learn that lesson the hard way. With small disruptions compounding delays across the manufacturing sector, and price pressures on raw materials remaining, it’s tough to find a strategy that will maintain the profitability of your firm.
When the manufacturing process also includes labor-intensive operations, the project can become a minefield to deliver on time. Deloitte’s manufacturing outlook for this year is positive, but accessing talent and economic uncertainty remains a challenge.
When it comes to optimizing your manufacturing operations, outsourcing your thermoformed product assemblies could help mitigate some of the risks you’re facing today. Let’s look at some of the benefits available from outsourcing thermoformed product assemblies and reducing your in-house labor-intensive operations.
Mitigate Project Risks by Outsourcing Your Product Assemblies with Labor-Intensive Operations
Any manufacturing process that depends on labor-intensive operations limits your potential throughput and stifles profitability. If you’re struggling to keep up with demand, attempts to speed up production could also lead to quality issues and increased scrap rates.
For decades, US manufacturers relied on lean strategies like JIT (Just-in-Time) to meet demand and manage costs. We now know that JIT carries inherent risk to manufacturers, especially if a portion of the supply chain fails to deliver. While some manufacturers are turning to a JIC (Just-in-Case) strategy, outsourcing manufacturing tasks as turnkey assemblies may be the better option.
Outsourcing is a better strategy than JIT and JIC because:
- Costs – JIC means stockpiling materials and hardware that increase the project’s cost without being justified by the volumes on order
- Delays – JIT is prone to delays, especially if you have to work with a limited number of suppliers
- Quality – Both JIT and JIC rely on suppliers to provide quality materials, some of which you’ll need to validate in-house for each lot
Turnkey manufacturing solutions from Kenson Plastics will help you mitigate the risks inherent in JIT and JIC.
Why Outsourcing Your Plastic Assemblies is the Best Strategy
Complex plastic assemblies (like transport interiors, aerospace parts, video bezels, or medical devices) often require labor-intensive operations to finish the product. Outsourcing assemblies to a turnkey manufacturer places all project responsibilities on one supplier. This makes it easier to coordinate all product requirements, leverage the latest manufacturing technologies, and avoid delays by accessing a larger network of raw material suppliers.
Kenson Plastics is a one-stop, build-to-print manufacturing shop. Our customers operate in tightly regulated markets such as aerospace and medical device assemblies. From tooling specification, material sourcing, and design optimization to project management, secondary operations, and quality validation, we support our customers every step of the way.
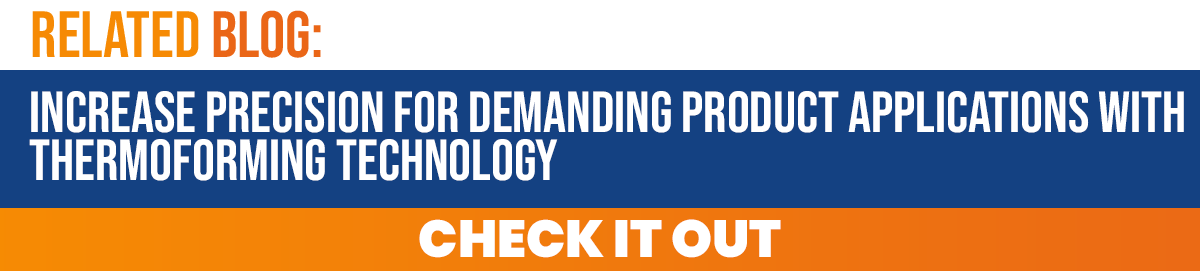
Take the Initiative and Start Outsourcing Your Product Assemblies with Kenson Plastics
One of the key trends that will define a product’s success over the coming decade is maintaining a sustainable manufacturing operation. This doesn’t just mean accessing the right materials, but also building a resilient production strategy that can survive (or ideally thrive) in an evolving market landscape.
Kenson Plastics can ensure you meet customer demand without sacrificing your profit margins. To read more about our flexible thermoforming practices, download this eBook with detailed information about our capabilities, processes, and services.
To establish a resilient manufacturing operation by outsourcing your thermoformed product assemblies today, reach out to Kenson and let’s talk.
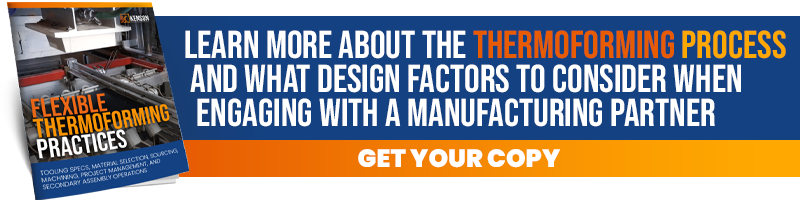