When working with self-service kiosks at low volumes, industrial designers and engineers need to remember that they still have a wealth of design and manufacturing options available.
Kenson Plastics can help find cost-effective alternatives to injection molding, providing you with many of the same benefits without the large capital investment you’d expect.
We can assist from the initial design phase of the kiosk’s interface area through the development phase of the actual enclosure. You won’t have to compromise on the fit or finish of your kiosk parts, and we can help make the manufacturing process economically feasible using a complex thermoforming approach.
Up-Front Design Considerations for Complex Thermoforming of Kiosk Enclosures and Parts
Designers should identify the critical features required and define the desired finish of the interface parts. Accurate matching of the different elements and materials, the color scheme, and the durability of the different parts should all factor into the conceptual design.
Kenson Plastics often works with customers who just have a rough idea of what they want. We work with them to build out a design by collaborating and iterating on the design of the parts.
To get you started, here are the key design considerations for using thermoformed parts in your kiosk enclosures:
Partner with Plastic Thermoforming Manufacturers Early
At Kenson Plastics, we know that the earlier we’re involved in the design process, the more value we can add to the project. We’ve even worked with concepts scribbled on napkins, and most of the time, that’s more than enough for us to get started.
We’ll need some additional information such as the environment (indoor or outdoor) the kiosk will operate in so that we can work out material selection and texture of the plastic. Once we know how durable the parts need to be, we can start thinking through any special features you’ll need. You also don’t have to limit your design to a combination of metal and plastic, as we’ve done full enclosures using large-sized, heavy-gauge plastics for customers like the post office in the past.
Get a Decent Grasp on Your Volumes
The more customized you want your kiosk enclosures to be, the more suitable complex thermoforming becomes. If you’re producing thousands of ATMs or self-service kiosks at a time, injection molding makes sense, but if your volumes are lower, thermoforming is the best way to go.
The thermoforming process is very flexible. We can assist whenever you have custom design requirements including, color variation, flexible branding and logos, or we can develop a generic thermoforming mold that you can reuse for a variety of kiosk designs and finishes.
You can really go anywhere you want with the kiosk’s design and finish and make it your own if you opt for the thermoforming process.

Design Tools and Molds to Service Multiple Clients
Kiosks are an efficient way for customers to help themselves in any number of service applications. The enclosures may be metal, but the customer interface area needs to be sleek and attractive while remaining functional and durable.
Customers who sell kiosk enclosures to different clients can work with us to develop a main enclosure mold and use the same tool design while customizing the color, logo, or internal fixtures and features. This can save on the tooling costs while servicing multiple clients in the industry.
Rethink Your Kiosk Design with Kenson Plastics
Kenson Plastics provides designers with a wealth of design options using a plastic forming process and high-precision machining of tolerances. Our engineers work with designers to find a cost-effective alternative to injection molding that delivers similar finishing and part matching capabilities. With self-service kiosks, you’ll want a sleek and sexy design that is still economical enough to produce at lower volumes.
To see what the possibilities are for your next kiosk design using complex thermoforming, get in touch with Kenson Plastics today.
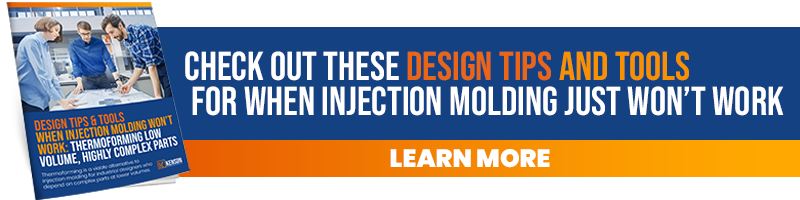